Breguet craftsmanship and watchmaking techniques
The art of watchmaking is at the very heart of the Maison’s craft with more than thirty different decoration methods and watchmaking techniques coming together to adorn their timepieces. The components crafted are often visible through a crystalline caseback but Breguet, as a prestigious watchmaker, applies the same finishing even to elements that are not visible, leading to the creation of exceptional timepieces.
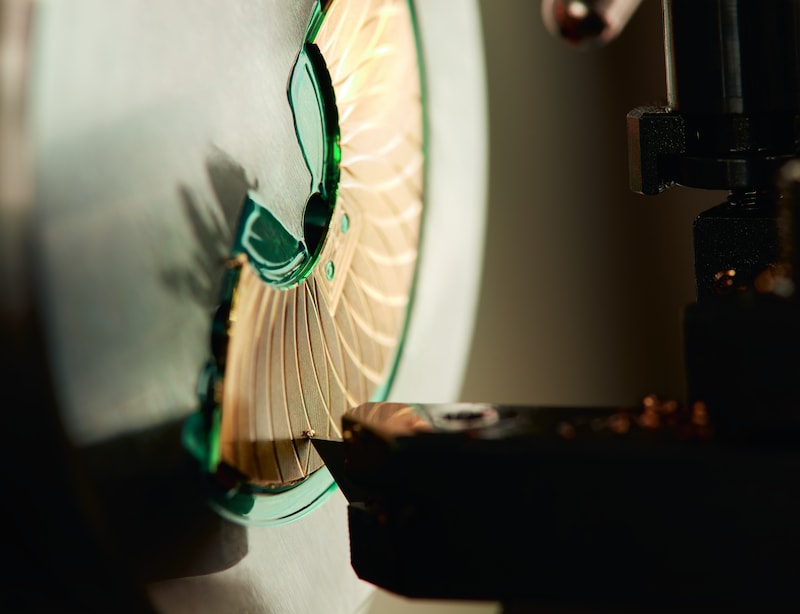
Craftsmanship
Ingenious watchmaker, A.L. Breguet was also a pioneer in the field of design. His inventions were aimed at making the information on the dial more legible, leading him to adopt a technique that had been used to embellish luxury creations since the 16th century : guilloché. Breguet applied it to its dials to counter the effect of light rays on smooth surfaces and thus improve legibility. A signature of fine watchmaking, today this decoration is applied by hand by the Maison’s artisans to the dials, rotors, mainplates and casebacks. These components are made of the finest materials such as gold, platinum or mother-of-pearl.
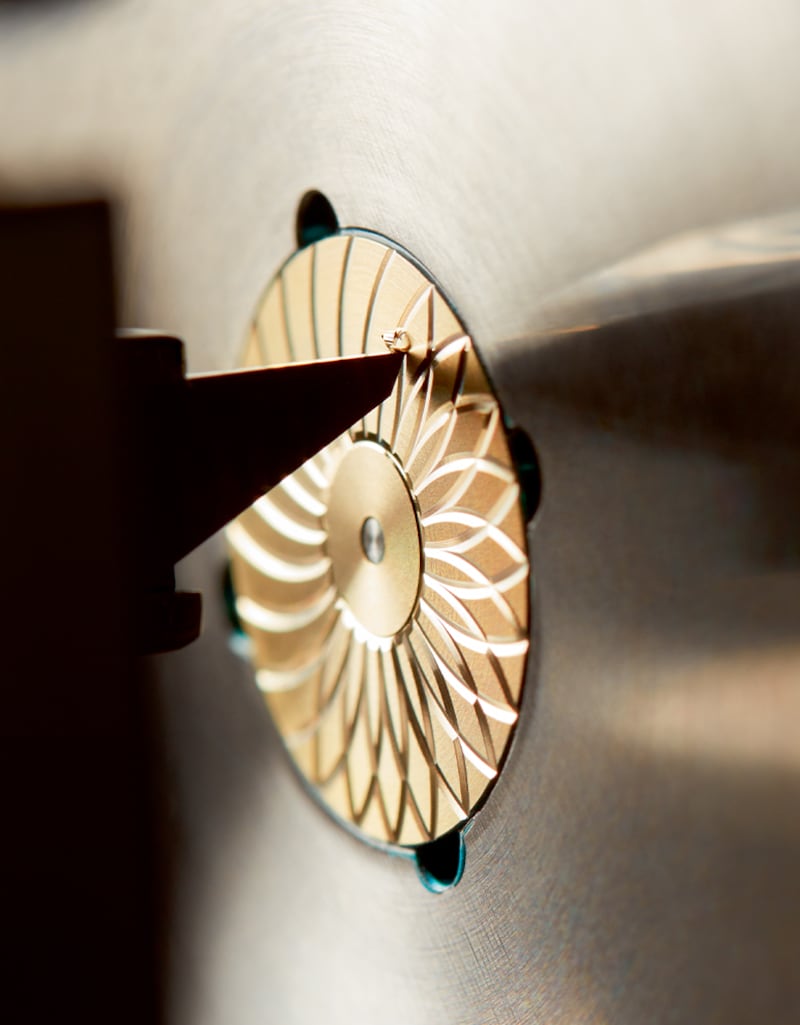
Engraving is an ornamental art form in its own right. The master engraver sculpts the finest materials free hand, using a range of tools that have been meticulously shaped and adapted to their hand. The surfaces are shaped, creating reliefs with precision, care and patience, aware that the slightest slip of the hand can undo several days’ work. The resulting finishes give Breguet watches an unparalleled elegance and unique identity.
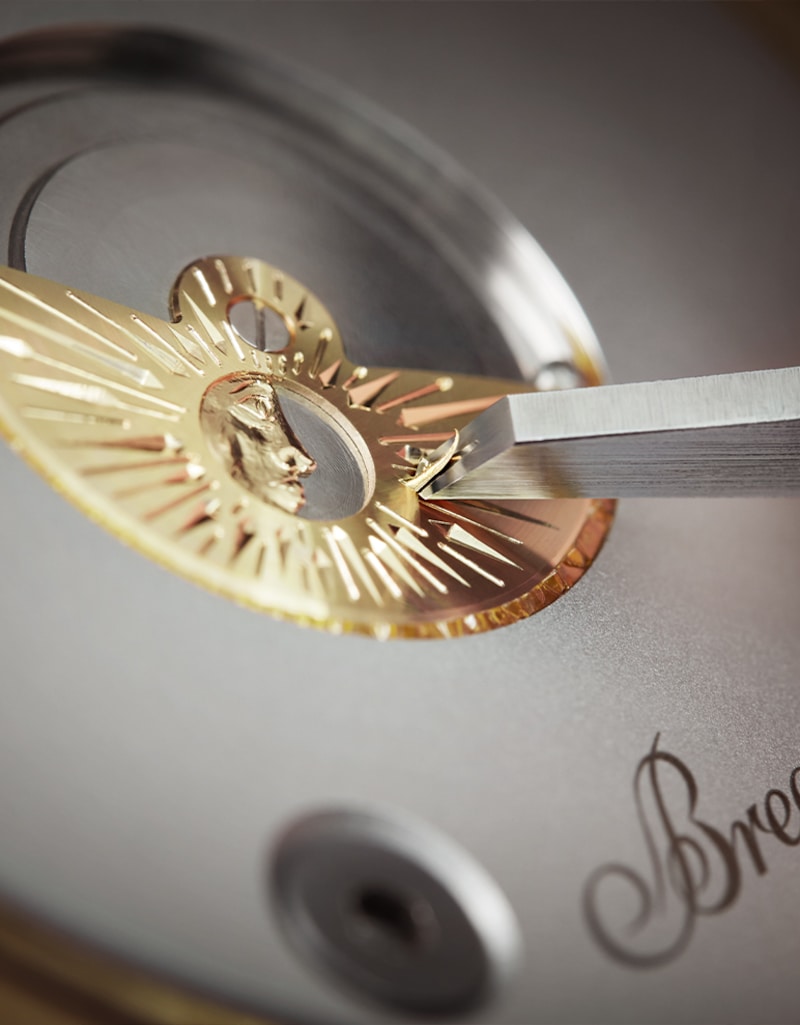
More than simply decorating the dial, this is a highly specialised craft that requires discipline, patience and technical mastery. The process begins with first crushing and then grinding the enamel to a fine powder. Once this powder is calibrated and purified, it is then applied in layers with a brush to embellish the creation, grain by grain, in a series of stages depending on the desired finish (translucent or opaque). The artisan must anticipate the possible distortions and adapt their technique according to the shape of the pieces they are decorating, bearing in mind that the changes in certain oxides during the high temperature firing process may cause colour variations. This means that extra special attention is required for each firing. The last step of this meticulous process is to apply the finishing touches to the piece to ensure that it adheres to the pre-determined standards and quality criteria set by Maison Breguet.
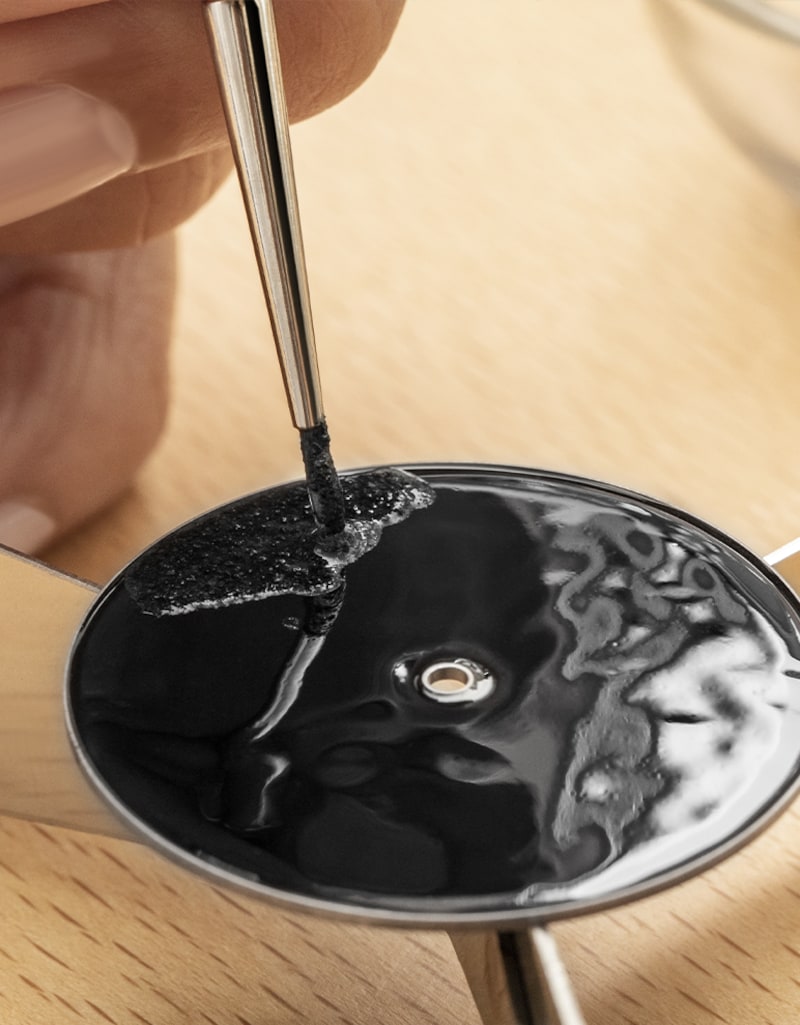
This decorative art consists of embellishing certain parts of the watch with precious stones. They are attached using subtle, discreet metal claws cut directly into the material itself. Breguet uses several gem-setting techniques such as snow settings, which aims to reduce the visibility of the surface on which the stones are set, or invisible settings for baguette-cut diamonds.
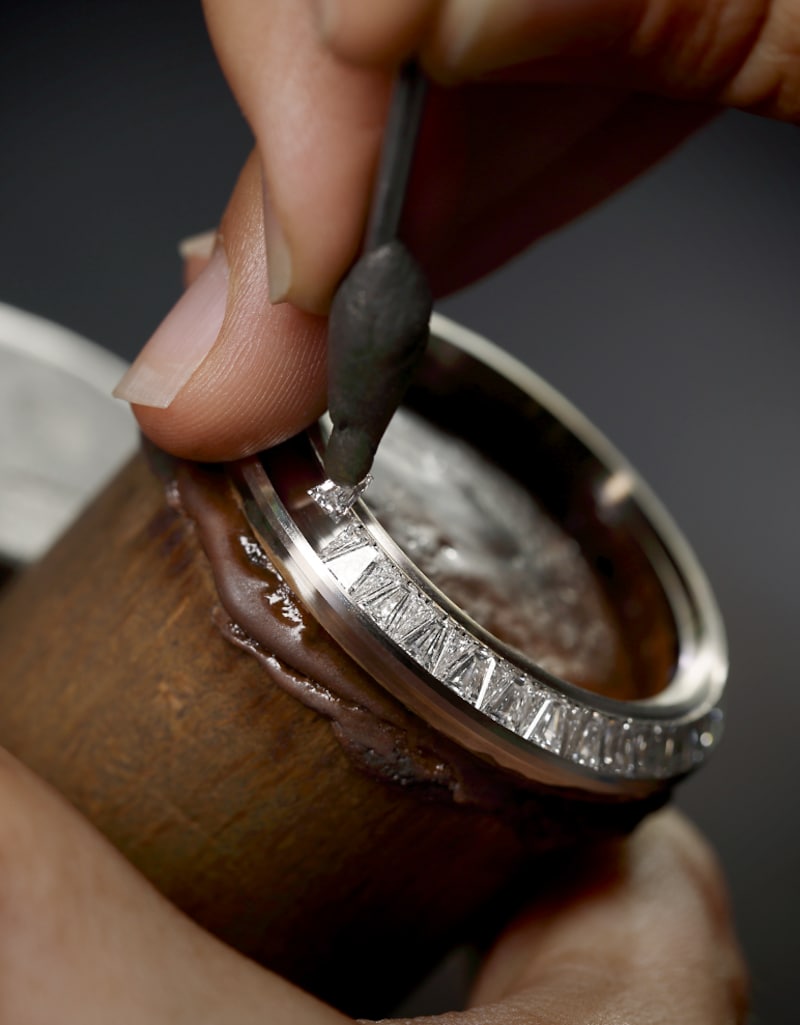
The art of cameo engraving is over 4,000 years old, and is one of the most exceptional of all the techniques. It is made from shells with contrasting layers of colour. The artisan, using a personally hand-crafted chisel, works the inner layers of the shells to a thickness of just a few millimetres, creating an exceptionally fine and detailed design. The master engravers only work with the finest shells in the most exquisite shades.
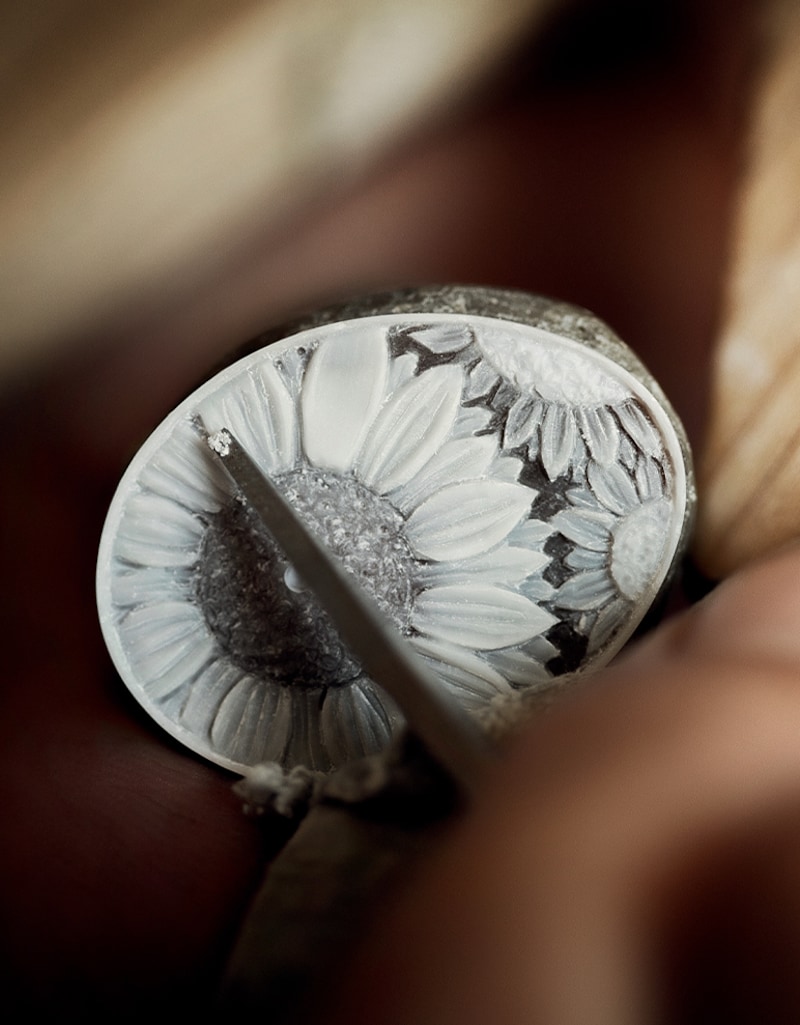
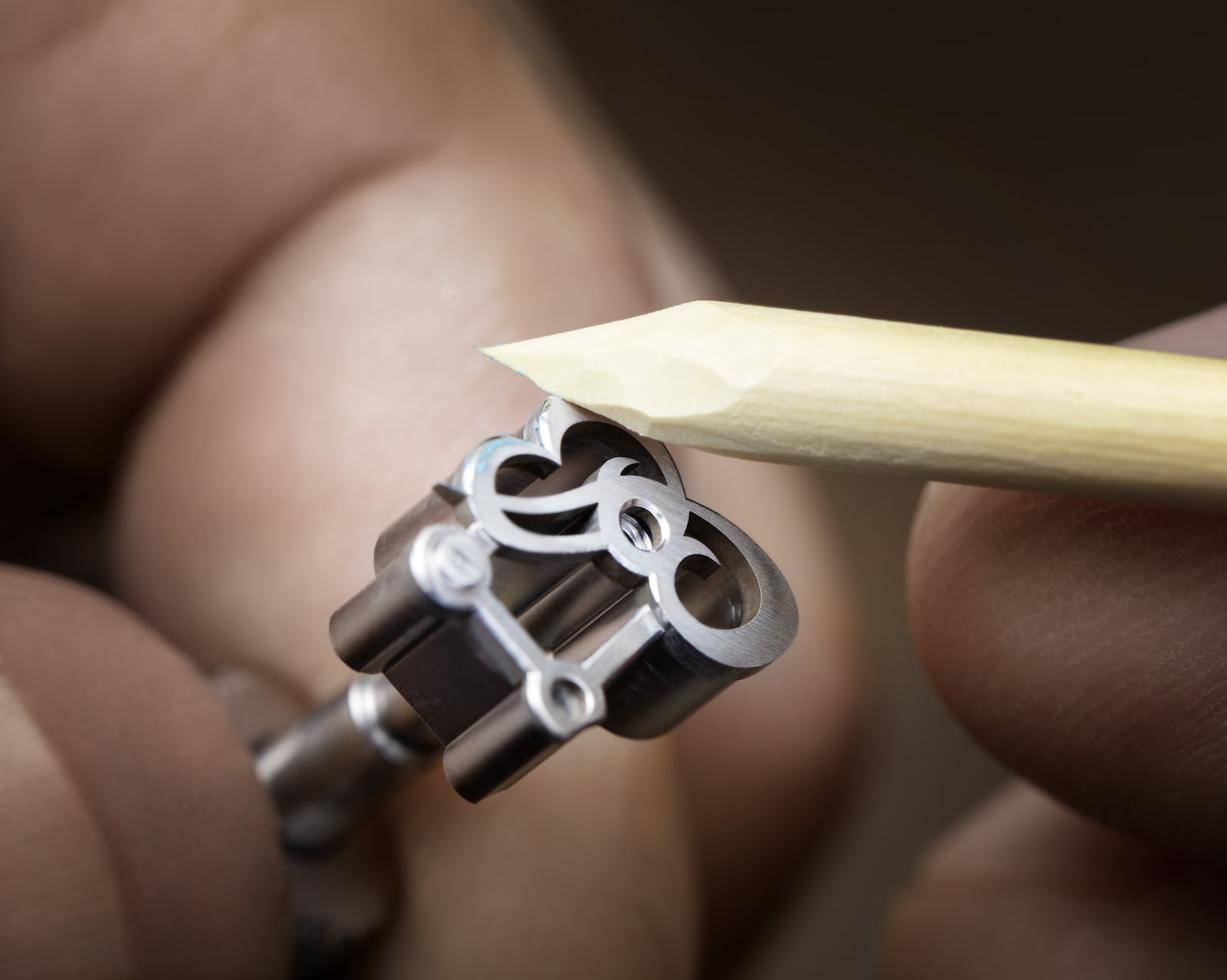
Watchmaking techniques
Anglage, one of the finishing techniques that relies on skills being handed down from generation to generation, is characterised by its complexity. Used for shaping and polishing angles, normally at 45°, anglage, also known as bevelling, serves two functions: the first is is practicality, as it eliminates burrs and machining marks that could be detrimental to the operation and reliability of the movement, but above all it serves an aesthetic purpose, thanks to the subtle interplay between the shine of the satin-finished faces and the polished angles. Each surface is reworked by hand, altered and then polished using several tools and abrasive materials in order to achieve the smoothest of finishes.
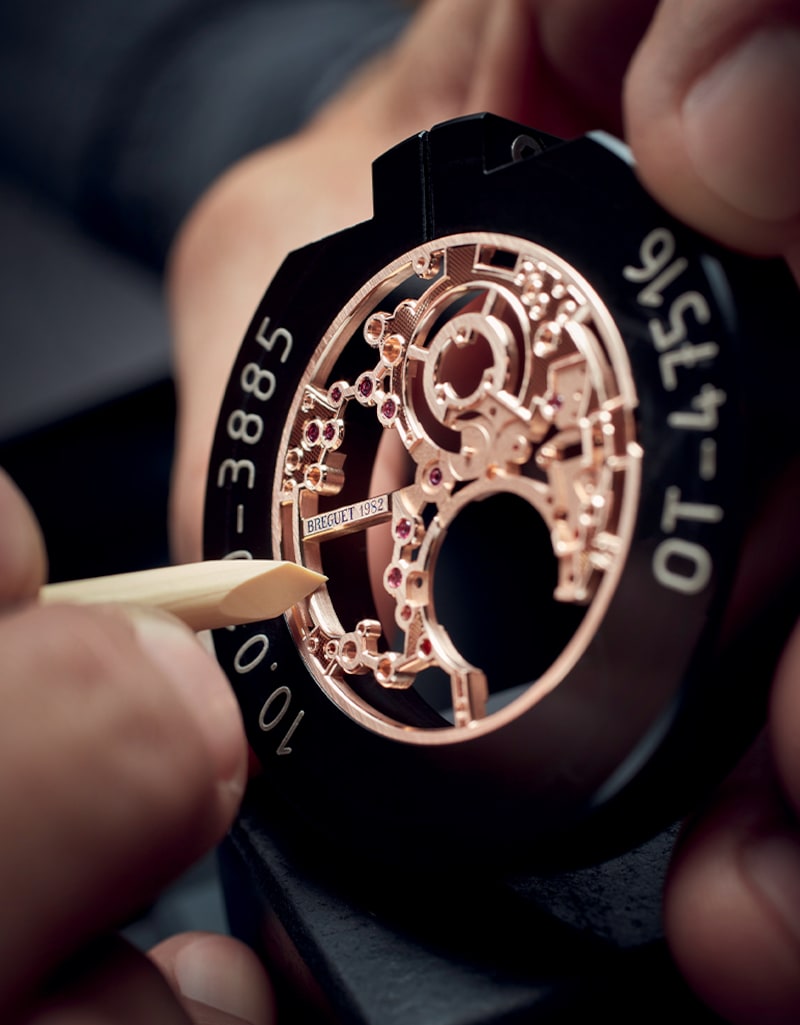
This pattern is generally used on the barrel cover and sides of the bridges. The design takes the form of a spiral that unfurls from the centre of the piece. This is done using a circular finishing brush that delicately traces the contours of the spiral onto the flat surface.
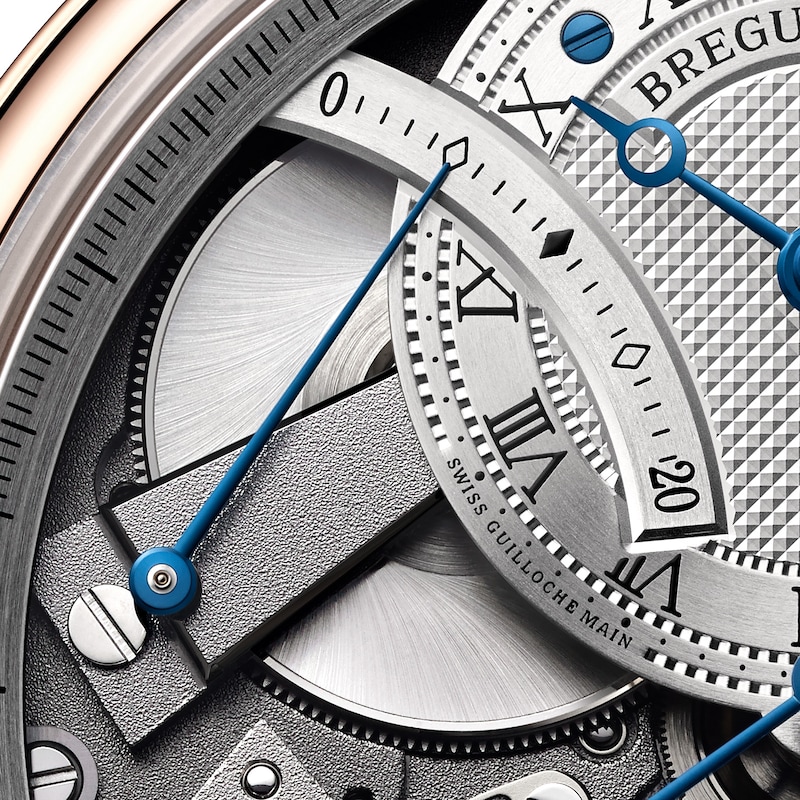
Beading consists of embellishing the flat surfaces of the mainplates and bridges with small loops or circles. While these patterns are aesthetically pleasing, they are also functional as the distribution of the loops is a result of artistic research which helps to prevent oxidisation and removes machining marks.
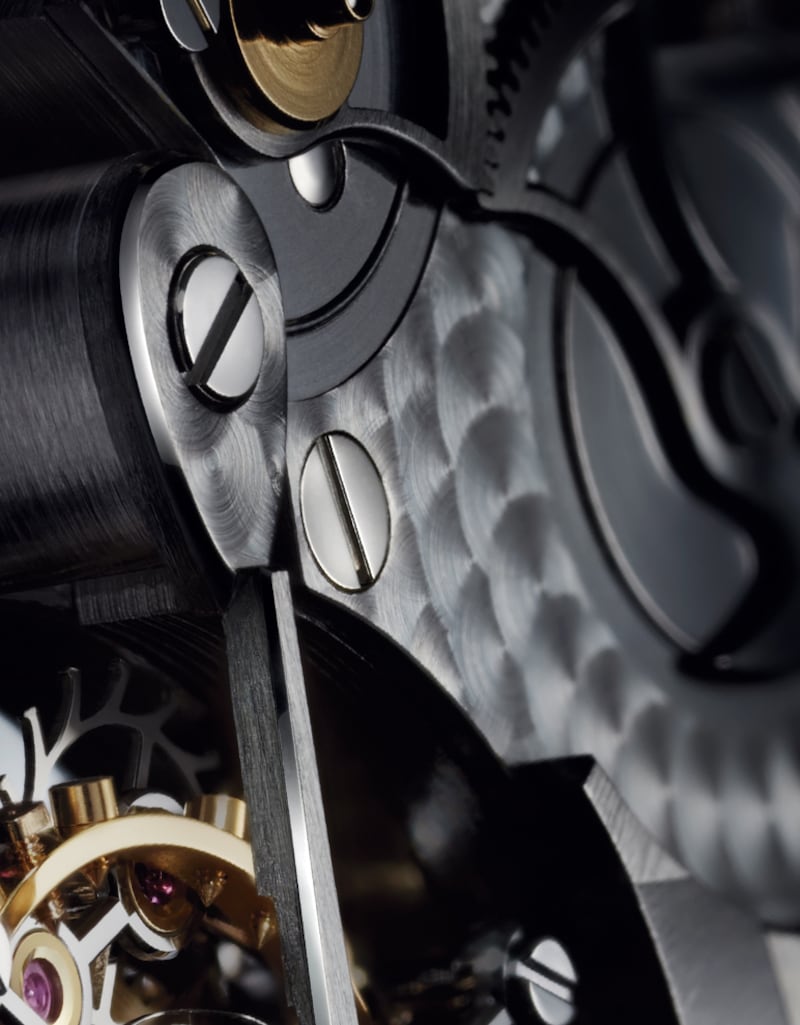
This craft is used to enhance manufactured metal parts by eliminating any irregularities and burrs, leaving a smooth, shiny finish. The parts exposed to light and wear in particular are polished. Various techniques are used throughout the creation process of a Breguet watch in order to to obtain finishes ranging from a flat polish to an ultra smooth finish, or even to create radiant rounded curves.

Also known as côtes de Genève, this technique consists of creating lines or stripes on a flat surface that are delicately separated by brushed areas. The remarkably beautiful straight ribs are an ornamental finish usually reserved for bridges.
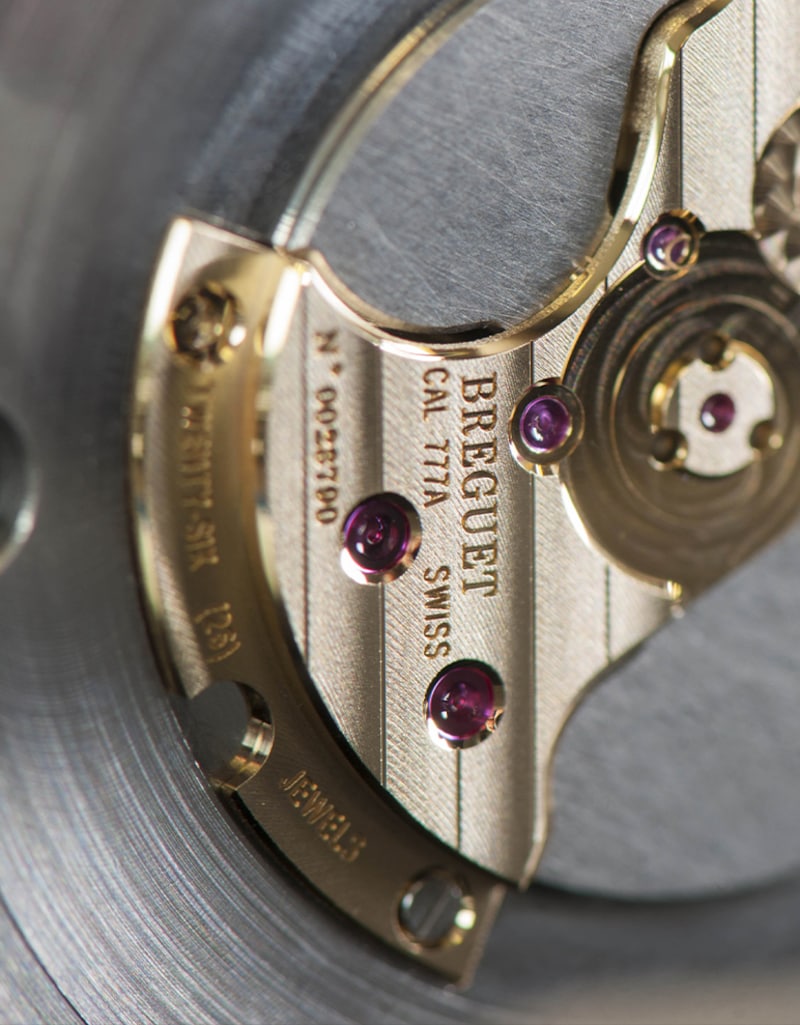
This finishing method consists of blasting micro-beads onto a given surface. The result of which is a matte-like finish that Breguet uses for the mainplates and bridges of its Tradition models in particular.
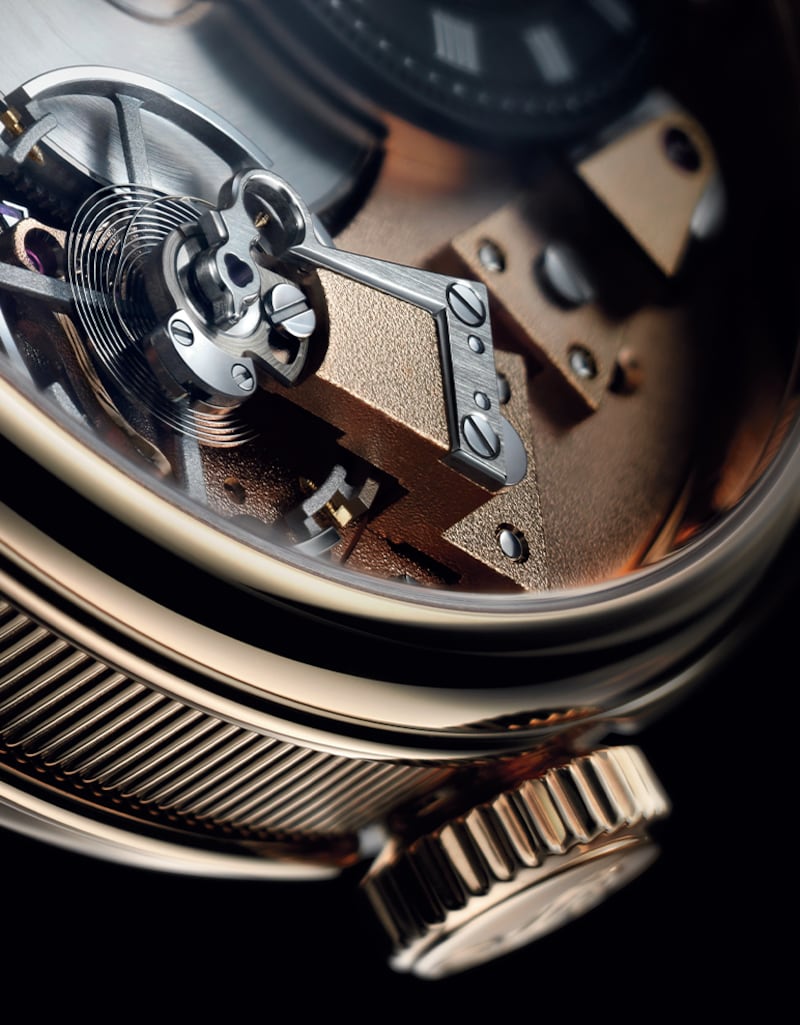
Similar in certain aspects to snailing, as it is applied to a flat surface using a circular brush, however, instead of producing a spiral design, sunburst finishing creates a pattern of straight radial lines starting from the centre.
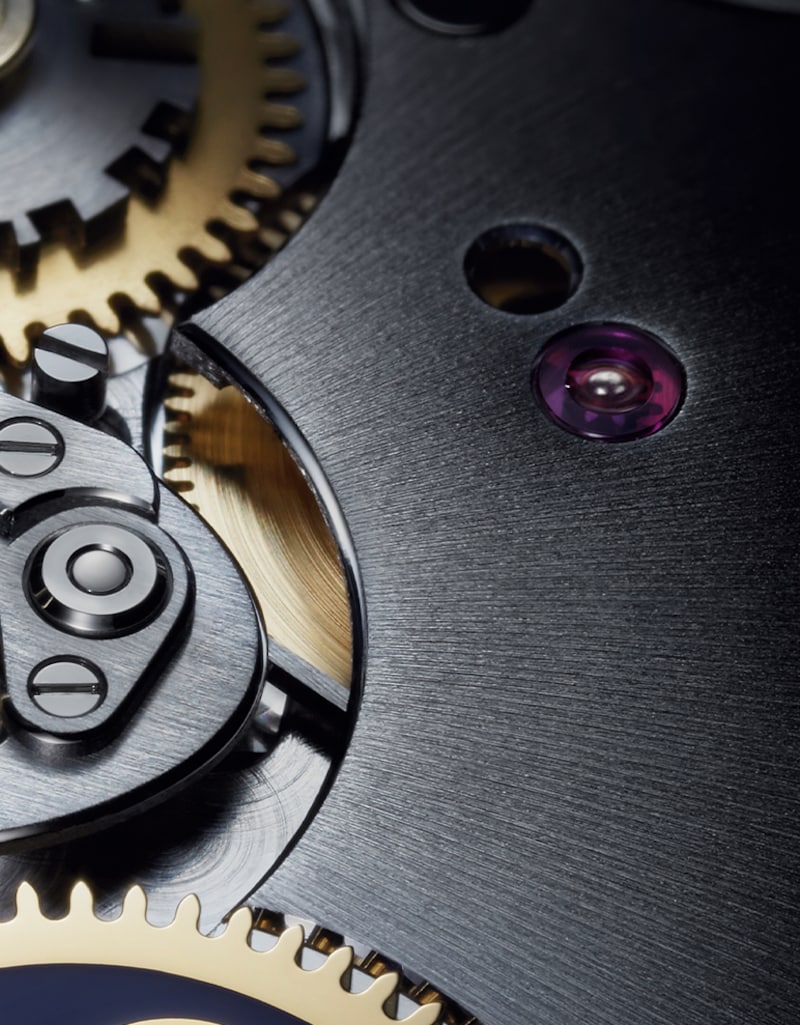
These techniques are used to embellish the moving parts. Stretching consists of satin-finishing the sides (vertical part) of a bridge or mainplate, most commonly using a grinder or file. The purpose of dressing is to satin-finish the top of a bridge or swing lever, generally using sand paper, a file or a stone.
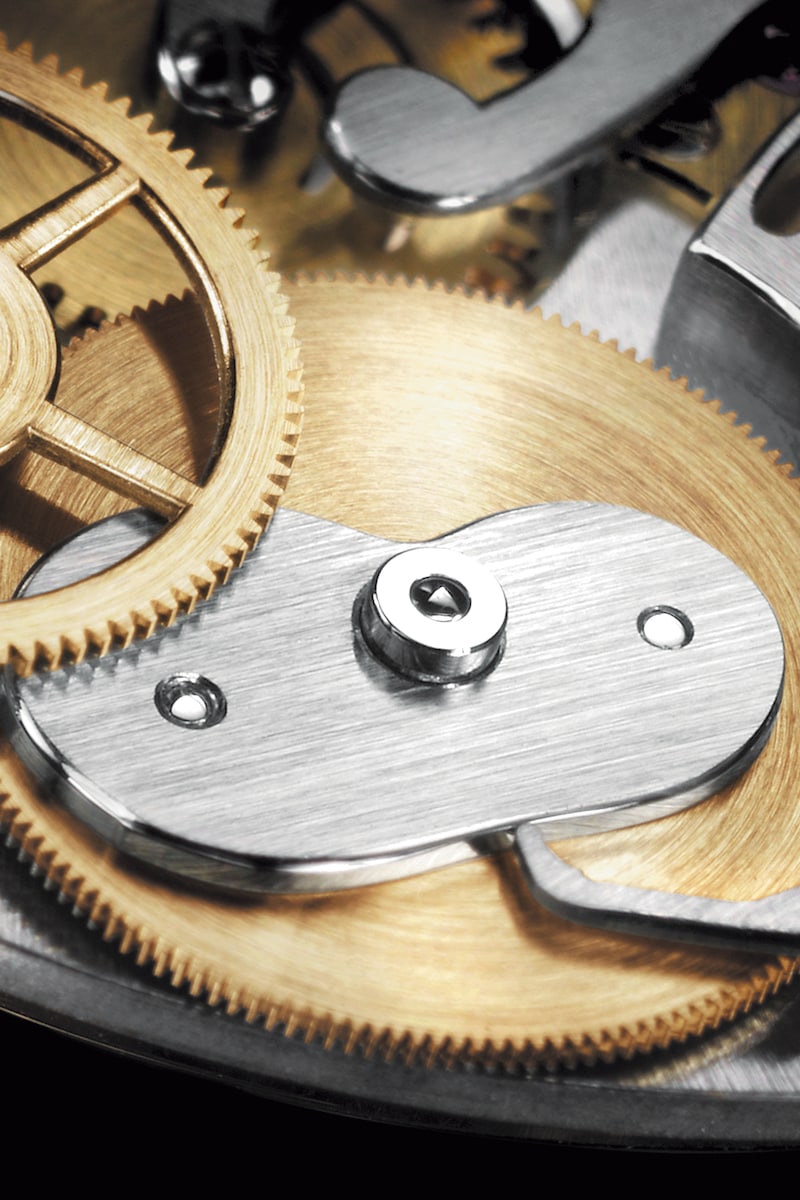
Decoration handcrafted using a diamond cutter. The material is delicately engraved to reveal reflections and reliefs, achieving a sparkling frosted appearance. Although the process is identical for all pieces, the final result is unique, thanks to the artisan's personal touch and creative spirit.
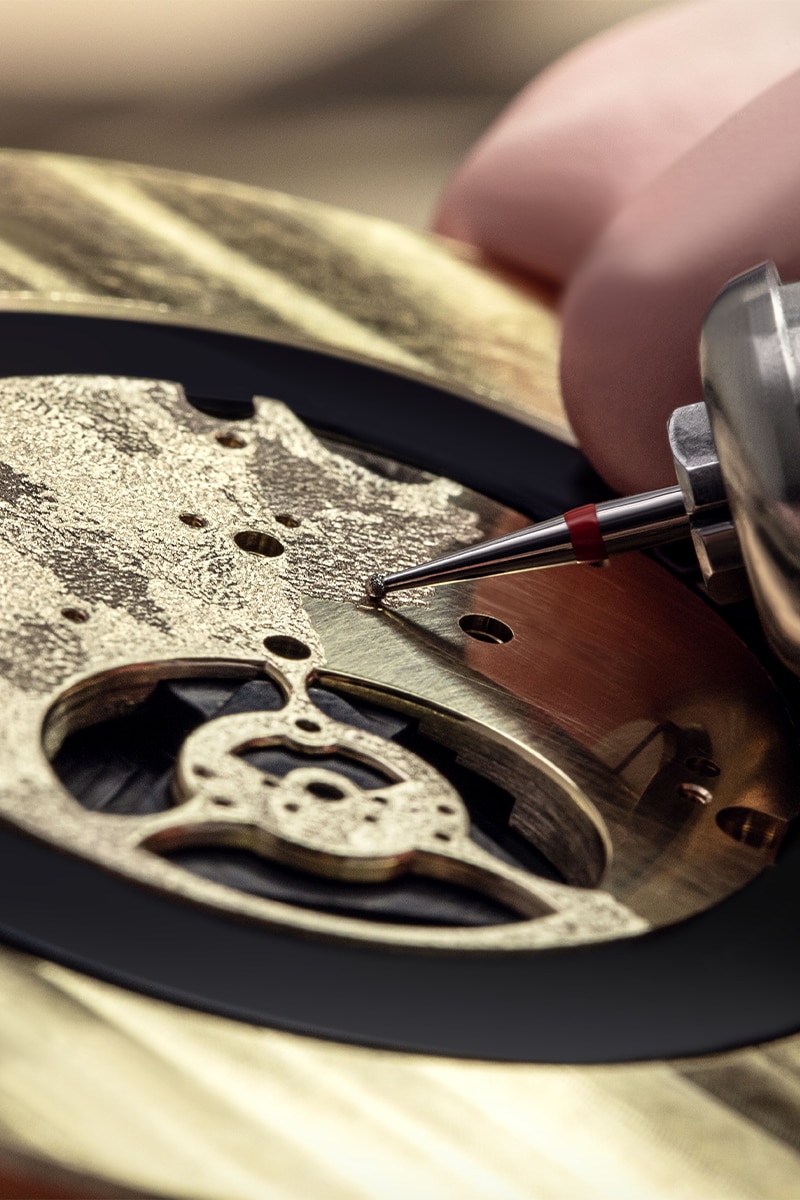